BRISK TECH ENGINEERS
CUSTOMER: BRISK TECH ENGINEERS, BANGALORE
COMPONENT: SHAFT
OPERATION: OD – TURNING & KEY WAY – MILLING
COMPONENT MS BAR:
- TYPE 1 – COMPONENT OD 25.4 mm X LENGTH 1232 mm, WEIGHT 5KG
- TYPE 2 – COMPONENT OD 32 mm X LENGTH 1015 mm, WEIGHT 6.45KG
REQUIRED ACCURACY: RUN OUT 0.05 mm
BASIC REQUIREMENT: OD TURNING AND KEY WAY MILLING OPERATION TO BE DONE IN SINGLE SETUP
TO BE INSTALLED IN: SPECIAL PURPOSE MACHINE WITH TWO SPINDLES, ON THE LEFT (LHS Chuck) AND ONE ON THE RIGHT(RHS CHUCK). COMBINATION WITH MILLING ATTACHMENT
OUR SOLUTION: 3B 250Ø PER CHUCK WITH ONE SET OF SPECIAL HARD JAWS AND ONE SET OF SPECIAL TOUGHENED JAWS
CHUCK FEATURES:
The GMT PER Lathe Chuck
Our standard PER chuck has jaws which extend and retract to enable complete machining of shaft components in a single set-up.
Here the component is held between centres initially, (face driver at one end and tail stock support at the other end). Heavy cuts can be given by extending the jaws to clamp the shaft component.
Jaws retract out and the face driver is used for finish turning, with minimal depth of cut.
APPLICATION
Two PER chucks are mounted on both spindle heads and the shaft component is held between centres.
The component bright bar with allowance on shaft outer diameter and end faces is machined and centred.
LHS chuck clamps with hard jaws, and then machining operation can done on the remaining portion- of the component. Drive is given only on LHS chuck. Then the retractable hard jaws are reversed, and the toughened jaws are extended to clamp the machined surface at the RHS end.
Here the drive is given only on the RHS side. Now the finish machining at the LHS side can be done.
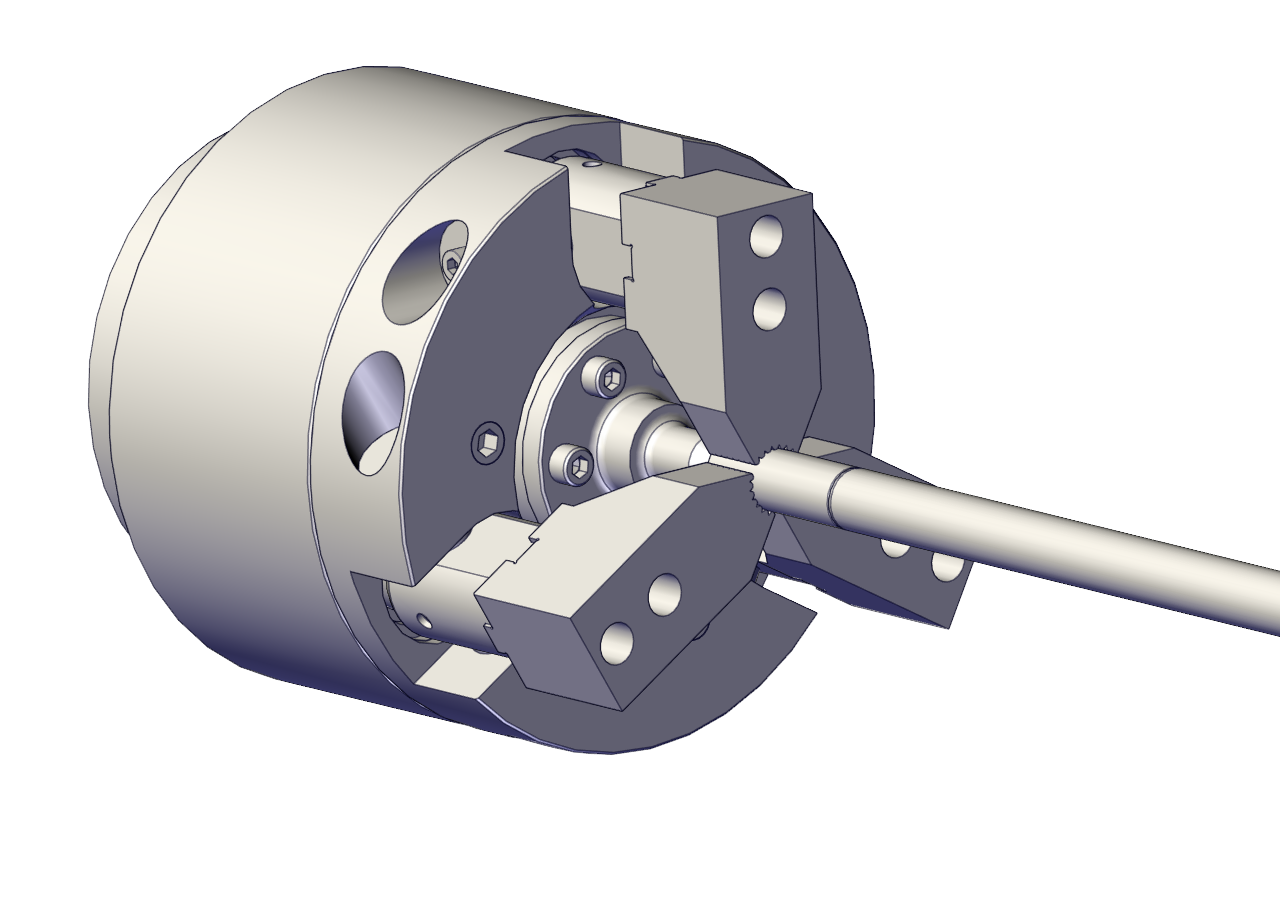